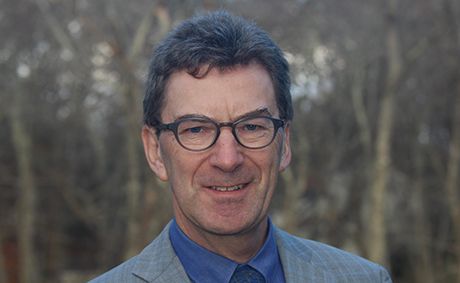
According to new research, quality has overtaken cost as a priority in plans for automating adverse event reporting. John Price reveals the drivers and barriers to change.
According to new research, quality has overtaken cost as a priority in plans for automating adverse event reporting. John Price reveals the drivers and barriers to change.
Although the COVID-19 pandemic has stalled progress with digital process transformation, many life sciences companies’ ambitions to apply smart solutions to rising pharmacovigilance (PV) workloads remain central to the investment agenda. These are the findings of Arriello’s second annual transatlantic survey among 200 professionals in senior roles spanning PV, Drug Safety and Product Safety departments looking at the industry’s PV automation intentions.
This year, quality overtook cost to become the primary criterion for automating PV workloads. Yet fear for human jobs, along with validation issues, persist as barriers to automation.
The context for the research is the shift in companies’ treatment of PV. A decade or so ago, as adverse event (AE) reporting workloads began to soar, companies across the pharmaceutical industry sought to reduce the cost of their operations — first by outsourcing and then by offshoring their activities. In more recent years, Pharma has begun to realize that any associated cost savings have come at the expense of quality. Now some are seeking to rebuild internal PV capabilities, despite higher costs and a talent shortage, by harnessing smart technology. But how far have companies come?
Automation intentions are strong
Unsurprisingly the pandemic has dominated decision-making over the last year which has been reflected in setbacks to automation initiatives. The proportion of respondents claiming to have PV automation solutions in place in 2021 was much the same as in 2020, despite around 40 per cent of last year’s respondents expecting to introduce automation within the coming year. Intentions remain strong, however. Only two per cent saw automation projects curtailed completely.
Whether categorized as robotic process automation (RPA), standalone PV automation, or PV automation as part of something bigger, up to two-thirds of companies claimed to have solutions “already in place” or were “likely” to do so in the next 12 months.
Yet it soon became clear that respondents were not typically referring to the application of smart solutions to end-to-end case processing (case collection, database work, triage, reporting). Rather, many seem to be leveraging IT to support isolated elements of case processing, such as auto-scheduling reports for submission and auto-narratives.
This is a shame, given the broader process automation opportunities now — for instance to simplify the work of reporters (healthcare professionals, patients), enabling them to make their reports directly into the PV database, circumventing the effort of data entry. This is similar conceptually to electronic data capture (EDC) in common use in clinical trials.
Our own observations suggest that many organizations employ EDC in clinical development, in electronically reporting safety cases to agencies, in generating auto-narratives, in program tabulations and listings for aggregate reports, and so on. This functionality is often included in the platforms provided by safety vendors and tends to add little in the way of new value to PV teams.
When the 2021 survey asked where companies planned to invest in smart (AI-enabled) or robotic process automation (RPA), clinical documentation management was the area most likely to have been automated already, followed by product quality compliance information handling and medical information management, then standard document compilation (forms, PSMF, aggregate reports, etc.). For investment over the next 12 months, literature screening and auto-narrative generation dominated plans: beyond that, smarter regulatory intelligence management and automated document compilation.
Yet, still, the figures are perplexing. AE reporting remains a high-pressure activity for pharma organizations and, in this year’s findings, 42 per cent of all respondents (rising to 48 per cent in the UK alone), claimed to have automated AE reporting solutions already in operation.
Yet our experience suggests that automation of end-to-end case processing is relatively rare in the industry. The high AE automation rates reported in the current survey are more likely to refer to very limited application, then — linked to specific elements of the overall AE processing system — rather than implementation of a novel, comprehensive platform to alleviate manual data management.
Quality trumps speed
To find out more, the research pushed for the drivers for investing in PV automation — finding that quality (cited by 71 per cent) outranked cost (cited by 63 per cent) by some margin, and was even ahead of speed of delivery speed (mentioned by 67 per cent).
Quality-wise, improved data quality is the chief objective, cited by 35 per cent of respondents — rising to 40 per cent among those in Drug Safety roles. For speed-related improvements, accelerated processing was the main benefit sought, cited by 34 per cent — rising to 38 per cent for Drug Safety teams, who also prioritized prompter reporting.
In terms of cost reduction benefits linked to automation, Product Safety teams were most likely to be seeking reduced infrastructure costs, and least likely to be targeting labor replacement.
Further probing, linked to existing capabilities, revealed that automation solutions clearly hold perceived value in a PV context, but that companies need the scope to increase and for the benefits to be more visible and easier to access. As one respondent noted in an open-ended response: “PV automation makes quality assurance easy. It’s just a matter of overcoming validation requirements and providing ease of access. Usability issues and fear of the unknown are what hold people back, which is a shame given that integrating functional events through PV gives awesome results.”
Familiarity, ease of use and cost – barriers to automation
In last year’s PV automation survey, the three top perceived barriers to PV automation were IT related. This year, although the familiar challenge of system validation remained a key concern, cited by more than four in 10 respondents (as in 2020), familiarity, ease of use and cost were the next most significant barriers to embracing new automation opportunities.
Fear of human replacement was a particular issue for PV teams (cited by 42 per cent of this cohort, in contrast to 22 per cent of those working in Product Safety). This suggests a misconception that job losses are inevitable when an automated solution is implemented, when in reality automation paves the way to retain talent which is currently considerably over-stretched.
A perceived lack of suitable solutions was cited as a barrier to adoption by 43 per cent of UK survey participants, compared to 27 per cent in the US. This further supports the conclusion reached last year, that there are differing perceptions of what constitutes ‘automation’ — i.e. that the technology and service provider industry must work harder to educate the market on emerging options.
That system validation still presents as such a high barrier to process innovation/ improvement is disappointing. PV professionals know how to validate a system and have the resources needed to monitor systems and confirm they are doing what they are supposed to do, with the quality and consistency required. This apparent barrier warrants further exploration, certainly, with a view to ensuring that it doesn’t go on to prevent take-up of more innovative IT solutions that could benefit PV teams enormously.
One of the next priorities for the industry must be to find ways round issues of system validation which continues to prevent companies from more readily capitalizing on the rapid evolution of next-generation automation capabilities.
PV and safety functions want to do more
Companies are clearly prioritizing quality and processing speed above cost now when exploring new automation options. There are encouraging signs that PV and Safety functions want to do more to advance the automation of their operations, and to improve the quality of data and the speed of processing/report delivery in particular. Accessible and user-friendly AE automation solutions — offering productivity benefits from day one — are supporting this goal.
Dr. John Price is an executive physician with 25+ years experience working across regulatory affairs and pharmacovigilance worldwide. He is a life sciences industry consultant and partner of Arriello, a provider of risk management and compliance services.
About the research
The 2021 Arriello survey was conducted by Censuswide in July/August. As in 2020, it polled 200 senior professionals in PV, Drug Safety and Product Safety functions across life sciences companies of all sizes, split evenly between the UK and US. The full report can be downloaded here.
"case" - Google News
November 16, 2021 at 08:40PM
https://ift.tt/3cgmt7J
Quality More Important than Cost: Building the Business Case for PV Automation - Pharmaceutical Executive
"case" - Google News
https://ift.tt/37dicO5
https://ift.tt/2VTi5Ee
Bagikan Berita Ini
0 Response to "Quality More Important than Cost: Building the Business Case for PV Automation - Pharmaceutical Executive"
Post a Comment